Company Profile
CV Support limited has been dedicated to researching and producing of virtual tracking support equipment for many years. Our product line includes virtual tracking head, rails, and jib/crane. Virtual tracking is essentially the tracking of a camera. The virtual tracking equipment provides the real camera’s position and angle to server in real space. According to these data, the virtual tracking software combines the virtual scene with the real image to generate realistic video output with a mix of virtual and real elements. There are two types of virtual tracking solutions: trackless and tracked tracking solutions. Our company uses tracked tracking solution based on high-precision sensors.
Compared to other tracking solutions, tracked tracking offers the following advantages: Firstly, it is environment independent. Whether the lighting is bright or dim, or whether the image is obstructed, it does not affect the tracking data. The shooting angle range is determined by the support equipment and is unrelated to the external environment. Secondly, since the tracking data is obtained by collecting internal sensors, there is no need to set up additional equipment at the shooting site, which is precisely what most trackless tracking solutions require. The tracked tracking system has no special requirements for the site, making it easy to set up, and more adaptable. Thirdly, because tracked tracking equipment is a hardware device, the amount of computation required for tracking data is very small, allowing it to provide a set of tracking data for each frame in real-time, without time delay, and data drift. Compared to trackless tracking, tracked tracking equipment is more reliable. Finally, trackless equipment typically requires separate support equipment for the camera and during setup, the trackless equipment’s position and angle detection device needs to be tediously configured with the camera. In contrast, the tracked tracking equipment itself is the support equipment, and many parameters are already set during the manufacturing process, making the setup of tracked equipment more convenient.
As one of the earliest camera tracking solutions, tracked tracking has unique and irreplaceable advantages. Despite the continuous emergence of trackless tracking technology and solutions, tracked tracking equipment remains the first choice for users who pursue stability, efficiency, convenience, and cost-effectiveness.
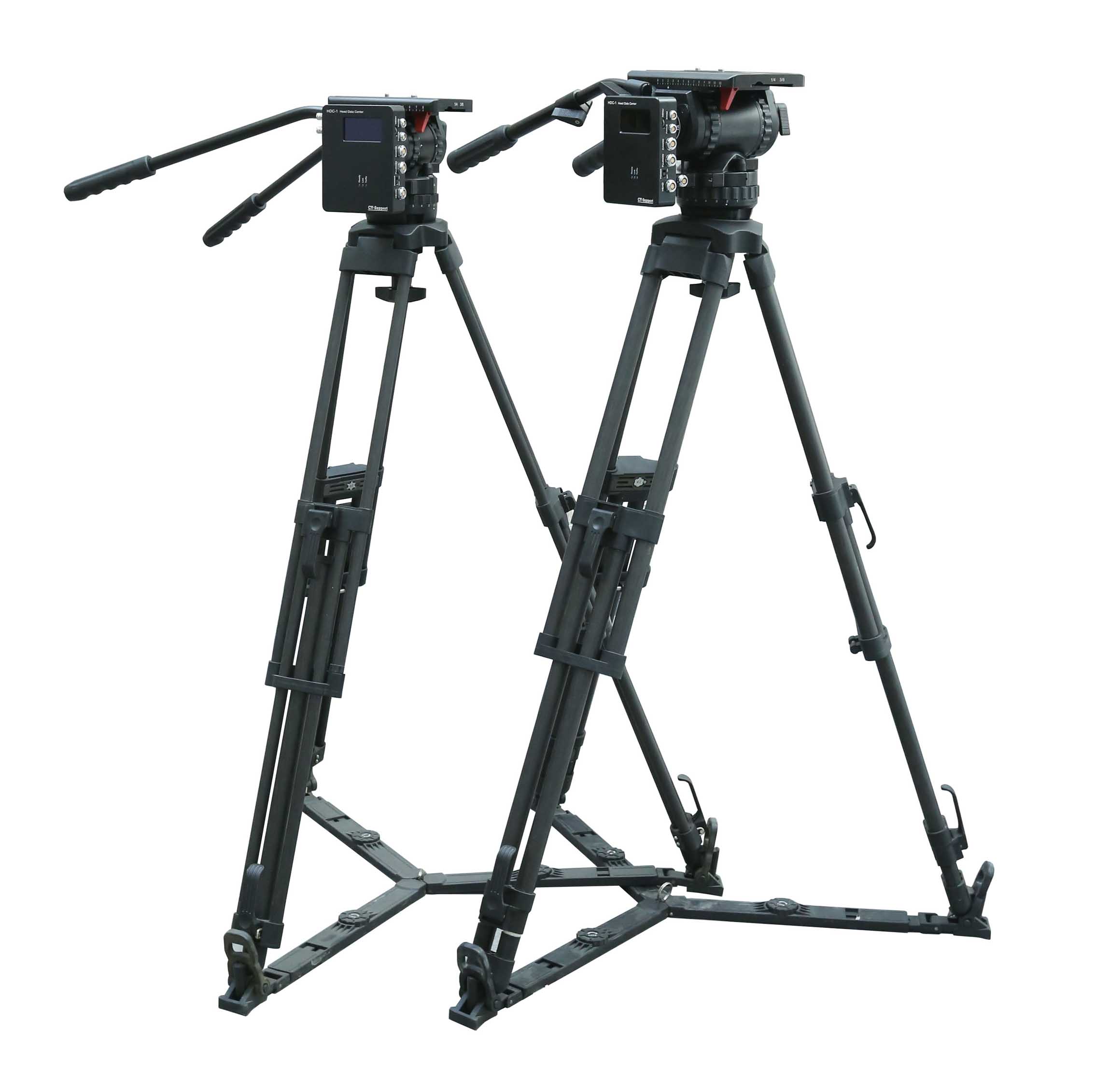
VR Tracking head instruction
CD15A/CD20A tracking head not only provides the server with camera horizontal and tilt angle data, as well as camera lens data, but also offers a camera positioning function, supplying the server with the field of view (FOV) vertex (eyepoint) position.
The system has a wealth of adjustment parameters that can compensate for positional deviations caused by camera height, lateral movement, and forward/backward movement. It can also compensate for angular deviations that occur during camera installation.
In addition to standard horizontal shooting, the system also supports vertical shooting. To enhance data accuracy, the head is equipped with a high-precision digital level. The system includes an angle and offset measurement function for the lens FOV angle.
Regarding lens data, the system not only features a sensor for reading semi-servo lens data but also provides a full-servo lens data interface and is compatible with cine lenses.
All positioning data can be saved, allowing the system to retain its previous state upon reboot without requiring recalibration. The system uses the FreeD protocol and transmits data to the server via UDP mode over the network.
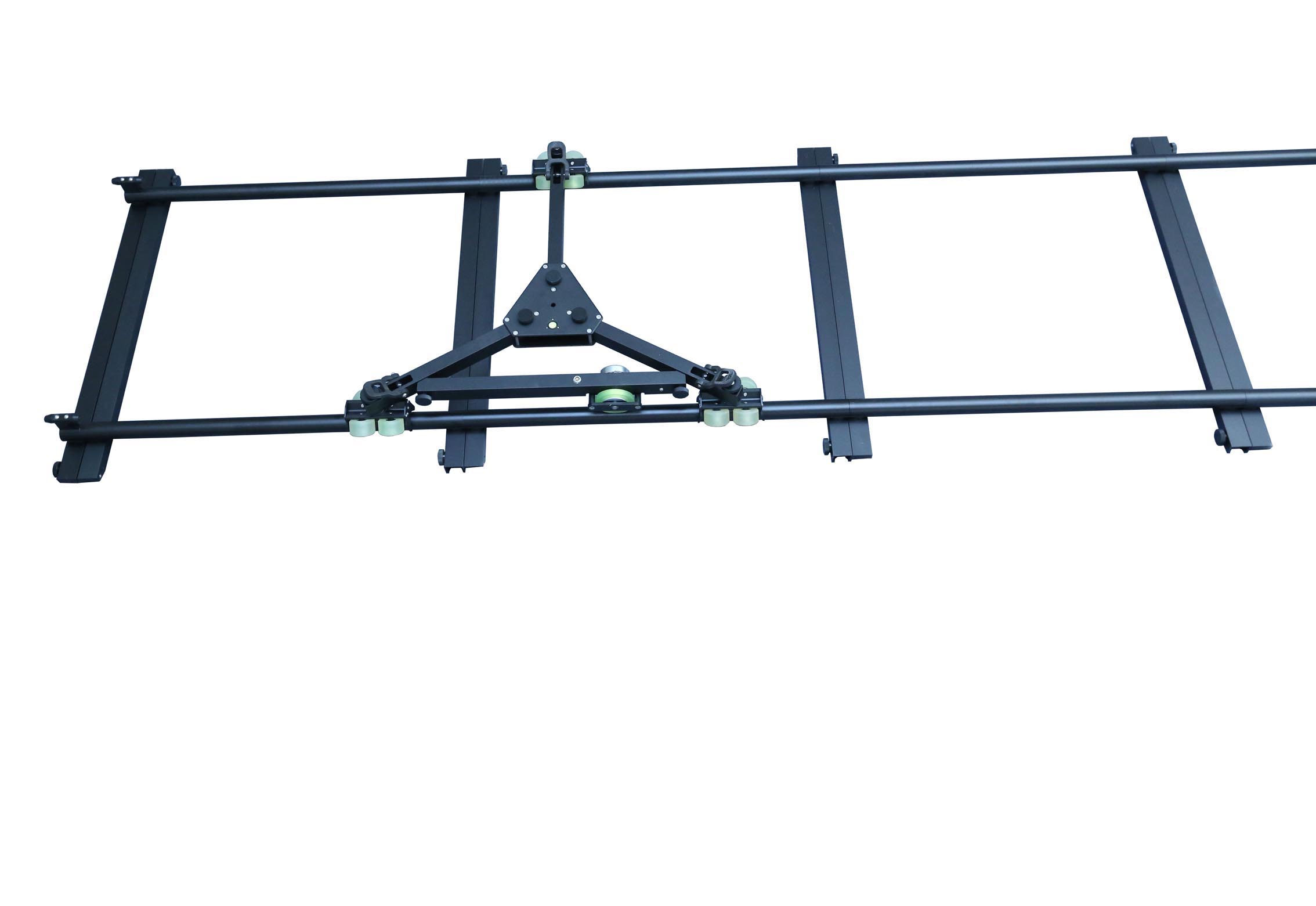
Virtual Tracking Rail
The TR50 virtual tracking rail, when equipped with the CD15A or CD20A virtual tracking head, provides users with a linear moving camera position.
The rail design fully considers the requirements of being lightweight yet sturdy, portable, and easy to install. Thanks to the use of high-precision track wheel sensors, the tracking data of the rail system does not depend on external environmental factors, ensuring precise tracking data even over long distances and large areas.
The system provides a convenient method for users to quickly determine the rail’s position and azimuth data on-site, achieving a tracking accuracy of up to 1 cm.
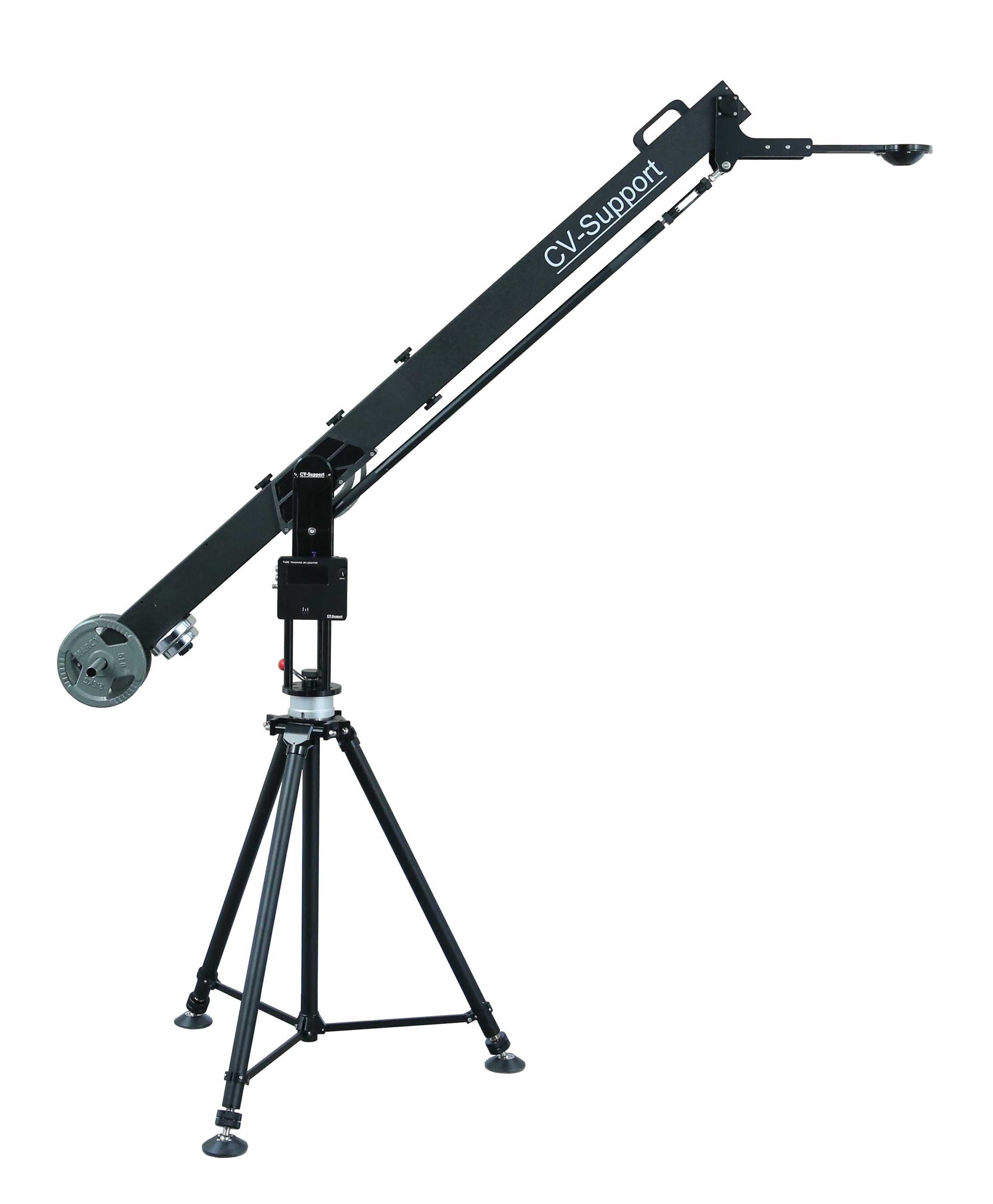
The TJ20 virtual tracking jib is a manually operated jib specifically designed and manufactured for virtual production needs. When combined with the CD15/CD20 virtual tracking head, it provides a flexible virtual tracking camera position for small studios.
To meet the precision requirements of virtual production, especially for XR (LED screen) applications, the TJ20 virtual tracking jib is equipped with high-precision sensors. Compared to ordinary manual jibs, it features a sturdier and more robust structure, along with a high-precision leveling bubble and fine adjustment mechanisms, making horizontal adjustments more convenient and accurate.
As a track-based tracking system, the TJ20 virtual tracking jib does not have special environmental requirements. It does not require additional positioning markers, and variations in ambient lighting or obstructions do not affect the continuity and accuracy of tracking data. Moreover, it imposes no special restrictions on shooting angles. Therefore, in the fields of VR, AR, and particularly XR (LED screen) virtual production, where camera mobility is crucial, the TJ20 virtual tracking jib system offers a highly cost-effective solution.
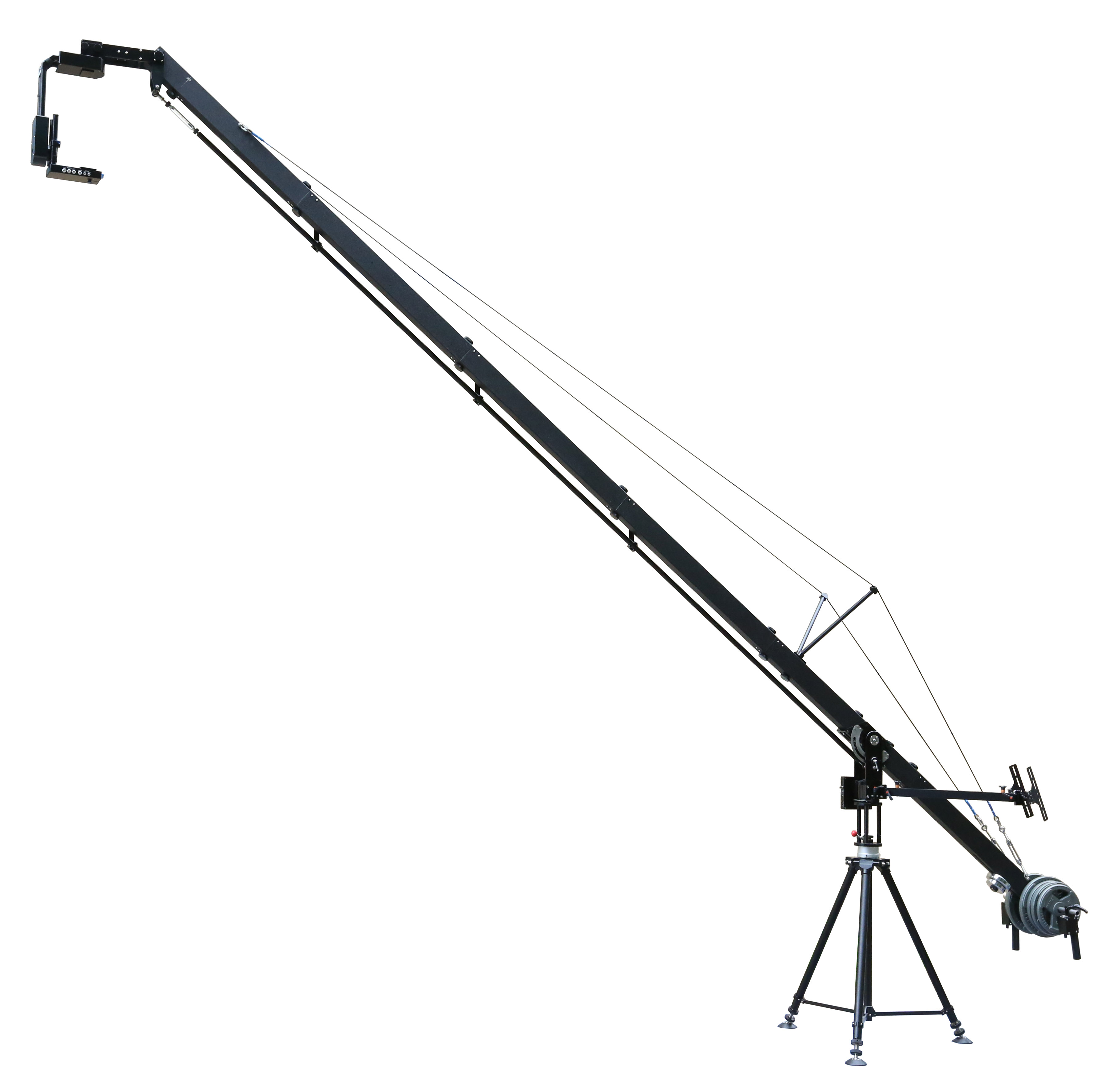
Virtual Track Jib
The TJ10 virtual tracking jib, in particular, is an remote head jib designed specifically for virtual shooting needs. It is equipped with industrial-grade high-precision angle sensors on the horizontal and tilt axes of the jib. The head is driven by high-quality DC servo motors and employs a redundant design to enhance stability during movement. It also features a lens control and data acquisition system that can control and collect data from broadcast servo and semi-servo lenses. The jib uses high-precision levels similar to those found in optical measuring instruments to ensure accurate tracking data throughout its entire range of movement. The TJ10 virtual tracking jib is not only used in virtual green screen shooting scenarios but is also particularly suitable for applications such as AR (augmented reality) and XR (extended reality with LED screens), where high tracking data accuracy is essential.
Additionally, the TJ10 virtual tracking jib is user-friendly in terms of setup and initial virtual tracking data parameter configuration. Each tripod leg is equipped with a screw adjustment device to ensure efficient high-precision setup in a short time. To facilitate quick and easy initial virtual parameter settings, the system uses a combination of software and hardware, providing real-time parameter adjustment in the virtual scene to achieve a "what you see is what you get" effect.